نگاه کلی بر سیلندر یا جک پنوماتیکی
- generalsanat_vahid
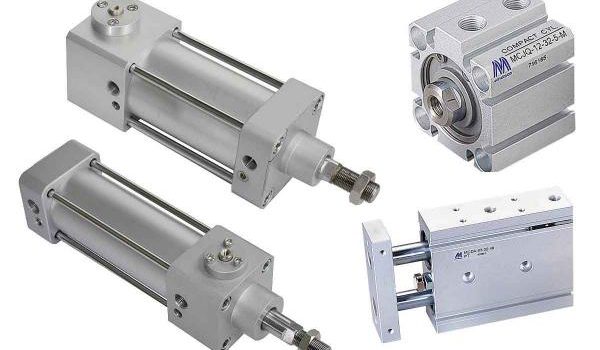
افزایش راندمان کاری سیستم های صنعتی
به دلیل الزامات رقابتی در بازار، سیستم های مکانیکی باید طوری طراحی شوند که عملکرد خوب و قابلیت اطمینان بالایی داشته باشند. پس از ارزیابی عوامل کلیدی طراحی یک محصول در مرحله طراحی، ویژگی های جدید اغلب به سرعت در یک محصول گنجانده شده و به بازار عرضه می شود. با آزمایش محدود یا عدم درک واضح از نحوه استفاده از یک طرح جدید توسط مصرف کننده، عرضه محصول با شکست زیاد می تواند بر برند سازنده تأثیر منفی بگذارد.
نقش سیلندر یا جک پنوماتیک
سیلندر یا جک پنوماتیک یک جزء مکانیکی است که می تواند در یک خط مونتاژ اتوماتیک در یک سیستم تولید انعطاف پذیر استفاده شود. همچنین می توان از آن در دستگاه تعویض ابزار یک ماشین ابزار استفاده کرد. برای جلوگیری از خرابی سیلندر پنوماتیکی در میدان قبل از عمر مورد انتظار، سازنده باید سیلندر جدید طراحی شده را به همراه استانداردهای ISO مناسب تأیید کند و/یا قبل از عرضه محصول آزمایشات لازم را برای قابلیت اطمینان انجام دهد.
نمونه تاثیر حیاتی سیلندر یا جک در صنایع مهم نظیر صنایع هوافضا
فاجعه شاتل فضایی چلنجر یک حادثه مرگبار در برنامه فضایی ایالات متحده بود که در 28 ژانویه 1986 اتفاق افتاد. این فاجعه ناشی از خرابی مهر و موم های O-ring استفاده شده در اتصالات تقویت کننده است که به طور نامناسبی برای تحمل هوای فوق العاده سرد زمستانی که در زمان پرتاب غالب بود، طراحی شده بودند. در نتیجه، چلنجر در 73 ثانیه پرواز خود را کاوش کرد و تمام اعضای خدمه کشته شدند. پیامد این شکست، توقف پرتاب شاتل به مدت دو سال تا زمانی که اصلاحاتی در طراحی O-ring انجام شد، بود. برای اطمینان از عدم شکست محصول در این زمینه، اجزای معیوب باید با استفاده از روش آزمایشی مانند ALT پارامتریک شناسایی و دوباره طراحی شوند، که می تواند مشخصات کمی (RQ) قابلیت اطمینان را قبل از معرفی سیستم به بازار ایجاد کند.
عوامل ایجاد نقص فنی در صنایع مختلف
عیوب مواد، مانند حفرههای بسیار کوچک و تماسها در صورت قرار گرفتن در معرض بارهای مکرر، ممکن است به دلیل خستگی شروع به از بین رفتن کنند. خستگی منبع اصلی شکست در عناصر فلزی است که تقریباً 80 تا 95٪ از تمام خرابی های ساختمانی را توضیح می دهد. خستگی در فلزات انعطاف پذیر به شکل ترک هایی ظاهر می شود که در مناطقی رشد می کنند که تنش می تواند متمرکز شود، مانند سوراخ ها، لبه های تیز، شیارها و غیره. این خرابی ها می توانند بر قابلیت اطمینان سیستم های مکانیکی مانند اتومبیل، هواپیما، کشتی، موتور و … راکتورهای اتمی یک روش تست خستگی شامل برخی از حالتهای تنش/زمان نوسانی است: تنشهای نوسانی، تنشهای مکرر، تنشهای معکوس، و چرخههای استرس تصادفی. خستگی همچنین ممکن است تحت تأثیر دامنه تنش چرخه ای، تنش متوسط یا نسبت تنش، R (=σmin/σmax)، که می تواند به عنوان نسبت حداقل تنش چرخه ای به حداکثر تنش چرخه ای بیان شود. برای اشکال دورهای، قلهها در حداکثر (سمت بالا) و حداقل (سمت پایین) بسیار مهم هستند. هنگام استفاده از یک بار افزایش یافته که می تواند به عنوان ضریب شتاب (AF) بیان شود، می توان از آزمایش عمر تسریع شده (ALT) برای شناسایی عیوب طراحی مانند افزایش دهنده تنش در سازه استفاده کرد.
ALT همراه با بلوک دیاگرام قابلیت اطمینان به عنوان روش دیگری مورد بررسی قرار گرفت. این شامل یک طرح آزمایشی برای سیستم، شناسایی مکانیکهای خرابی مانند خستگی، و استفاده از معادله اندازه نمونه، بارهای تسریعشده، و غیره بود. میکر راه های عملی متعددی را برای سازماندهی ALT پیشنهاد کرد. انجام یک ALT به مفاهیم زیادی مانند عمر BX برای طرح تست سیستم، یک توصیف ساده شده استرس زندگی، فرمول اندازه نمونه و مکانیک شکست نیاز دارد زیرا ممکن است به طور ناگهانی به دلیل اجزای شکننده در یک محصول خرابی رخ دهد. تکنیکهای تست معاصر ممکن است نتوانند نقصهای طراحی اجزا را در یک سیستم چند ماژول تکرار کنند، زیرا رویهها نمونههای اجزای ناکافی را ارزیابی میکنند و خستگی (خستگیهایی) را که واقعاً توسط کاربران در بازار برای اجزا ایجاد میشود شناسایی نمیکنند.
برای به دست آوردن یک طراحی قوی از یک محصول مکانیکی، طراحان از تکنیک های سنتی مانند مکانیک شکست و استحکام مواد استفاده کرده اند. مهندسان از مکانیک کوانتومی برای کمک به شناسایی خرابیهایی که از ادغام فضای خالی (MVC) در بسیاری از آلیاژهای فلزی و برخی پلاستیکهای مهندسی منشأ گرفتهاند، استفاده کردهاند. برای یافتن منبع خستگی یک محصول مکانیکی، میتوان از یک مدل استرس زندگی با روشهای طراحی سنتی و تکنیکهای مرتبط استفاده کرد تا به شناسایی خرابی قطعات الکترونیکی به دلیل نقصهای مواد یا ترکهای کوچک در زمانی که قطعات تحت فشار (مکانیکی) قرار میگیرند، کمک کند. . روش های المان محدود (FEM) ممکن است منبع خرابی را شناسایی نکنند. به عنوان جایگزین، روشهای دیگری مانند پایش سلامت سازه (SHM) وجود دارد که امکان تشخیص منبع خرابی را فراهم میکند. با این حال، بهدست آوردن دادههای تجربی برای محصولات چند ماژول دشوار است زیرا آزمایشهای گستردهای لازم بود.